“零廢料加工”:鋁型材機架精密下料與套料算法實踐
在鋁型材機架制造中,材料成本占總成本的30%-50%,而傳統(tǒng)下料方式因工藝粗放、排樣不合理,常導致材料利用率不足85%,產(chǎn)生大量邊角廢料。為實現(xiàn)“零廢料加工”目標,精密下料與智能套料算法的應用成為關鍵突破口。
精密下料的邏輯
通過高精度切割設備(如CNC激光切割)與數(shù)字化工藝的結合,將鋁型材切割誤差控制在±0.1mm內,減少尺寸偏差導致的二次損耗。同時,采用三維掃描技術逆向建模,匹配型材截面特征,避免因余量預留過大造成的浪費。
套料算法的優(yōu)化路徑
1. 多規(guī)格訂單動態(tài)排樣:基于混合整數(shù)規(guī)劃模型,將不同長度、截面的訂單需求拆解為數(shù)學約束,通過啟發(fā)式算法(如遺傳算法)生成全局優(yōu)排樣方案。某企業(yè)應用后,6米標準型材的利用率從82%提升至96%。
2. 余料智能復用:構建余料數(shù)據(jù)庫,利用圖論算法進行余料形狀匹配,實現(xiàn)跨訂單的殘料二次套用。某案例中,余料復用率提高40%,年節(jié)省采購成本超200萬元。
3. 實時工藝補償:在排樣過程中嵌入切割熱變形補償模型,動態(tài)調整切割路徑,避免因熱應力導致的型材報廢。
實踐成效與挑戰(zhàn)
通過部署智能套料系統(tǒng),頭部企業(yè)實現(xiàn)日均處理300+訂單的柔性排產(chǎn),材料綜合利用率達95.7%,切割工時縮減22%。但算法需持續(xù)優(yōu)化計算效率,尤其在處理非規(guī)則截面型材時,仍需結合人工經(jīng)驗進行局部調整。未來,AI驅動的自學習排樣系統(tǒng)或將成為突破方向,進一步逼近“零廢料”目標。
該模式不僅降低制造成本,更推動鋁加工行業(yè)向綠色制造轉型,單噸產(chǎn)品碳排放減少18%,契合雙碳戰(zhàn)略下制造業(yè)的升級需求。
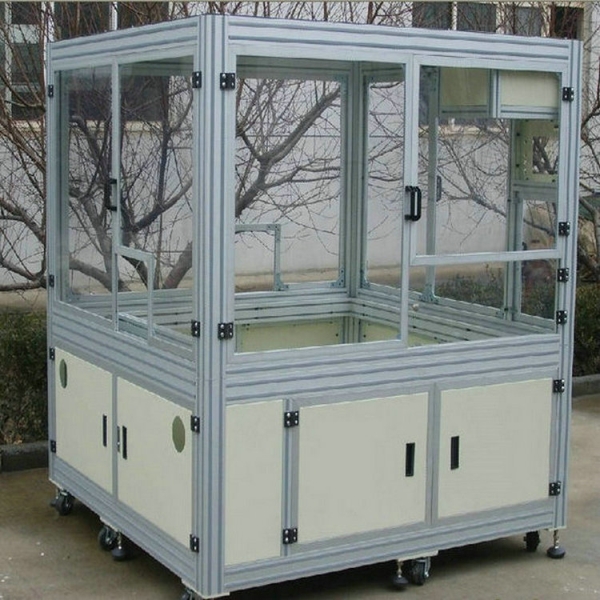